AB & NN:カンパーイ! (読者のみなさま、ごめんなさい。広い工場敷地内を案内していただき、筑波山や霞ヶ浦、反対側には晴れた日には池袋のサンシャインビルも一望できるという、展望棟にある試飲コーナーで、できたてのビールをごちそうになりました。でも、ご安心ください。一般の見学コースでも、最後はこの試飲コーナーに行き着きますよ!)
NN:おいしい! 味が濃いような気がします!
AB:これが、できたてのビールの味です。ビールは鮮度が大切です。このできたての味を消費者のみなさまにお届けするよう、アサヒビールでは受注、生産、出荷の期間を短縮するように努力を傾けているのです。
NN:(本来の取材にもどる)96年の段階で、98.5%再資源化できていたにしても、最後に残った1.5%の再資源化を実現するのには、相当なご苦労があったのではないかと思いますが……。
AB:まずは、意識改革です。分別容器に入れるのは、“ゴミではなくて資源である”という意識を社員にもたせること、容器を見ばえのよいものにしたのも、そのためです。再資源化の最大のキーポイントは“分別”です。さまざまなゴミを1か所に集めてしまうと、それを分別するのは容易なことではありません。最初の段階で分別させるのが、最も効率がよいのです。
完全に分別してあれば、リサイクル業者を見つけることが可能です。しかし、少しでもほかの廃棄物が入ってしまったら、業者は引き取ってはくれません。ですから、分別ステーションに担当者を決めて、分別収集を徹底してもらう。
それを今度は、分別センターでの担当が毎日チェックをします。朝礼のときに、それをフィードバックしてもらい、社員にもう一度注意をうながします。それの繰り返しです。習慣づけすることで、段々レベルが上がってきます。それと、分別しなければならないとなると、分別しやすいものを購入する必要性が生まれてきます。
NN:CGC委員会は、100%再資源化を達成した後でも開いていらっしゃるのですか?
AB:月に1回開いています。職場の係長クラス以上が参加しています。その場で指摘されたことを、現場に指示することのできる人でないとできませんので。
NN:分別の方法を社内公募されたというお話ですが?
AB:最初は、ポリエチレン、ポリプロピレンなどの材質によってわける努力をしてみました。しかし、プラスチックは、見ただけではその材質を知るのがむずかしかった。材質を特定する機器も購入したのですが、それに1つ1つの素材をあてて、調べるのはのは大変でした。もっと効率のよい方法はないのかということで、“ホップの袋”とか、ふだん使っている名前を利用することにしたのです。
いまでは、どのように分別したらよいかわからないものは、かならず総務のほうに連絡が入ります。そして、こちらで判断し、必要なら分解、分別をします。96年に100%再資源化を達成しているのですから、それから、だいぶレベルアップしています。自分たちで判断して、ボールペンも分解しています。
NN:処理をしてくれる業者をさがすのも大変だったのではないでしょうか?
AB:はい、当初は雑誌や発泡スチロールなど引き取ってくれる業者が見つからず、廃棄物の業界新聞で調べたり、廃棄物処理業者の展示会などに出向き、引き取ってくれる業者をたんねんにさがしました。
|
|
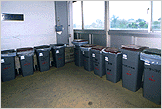
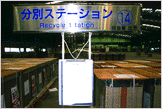
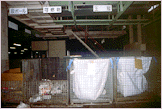
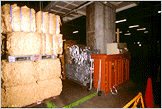
[写真・上] 誰でも分別しやすい容器 [中・上] 各分別ステーションには責任者の名前とチェックシート [中・下] 各ステーションから分別センターに集め、まとめる [下] できるものは減容・圧縮をする。圧縮機と圧縮された紙類。
|